CASE STUDY
3DEO’s Bone Scraper Part
Industry: Medical Device
Dimensions (mm): 15 x 10 x Ø 8

Customer's Problem
Producing a Small Complex Bone Scraper
The customer worked in the medical industry and needed to produce a small, complex bone scraper part for their bone cutter instrument in 17-4 PH Stainless Steel.
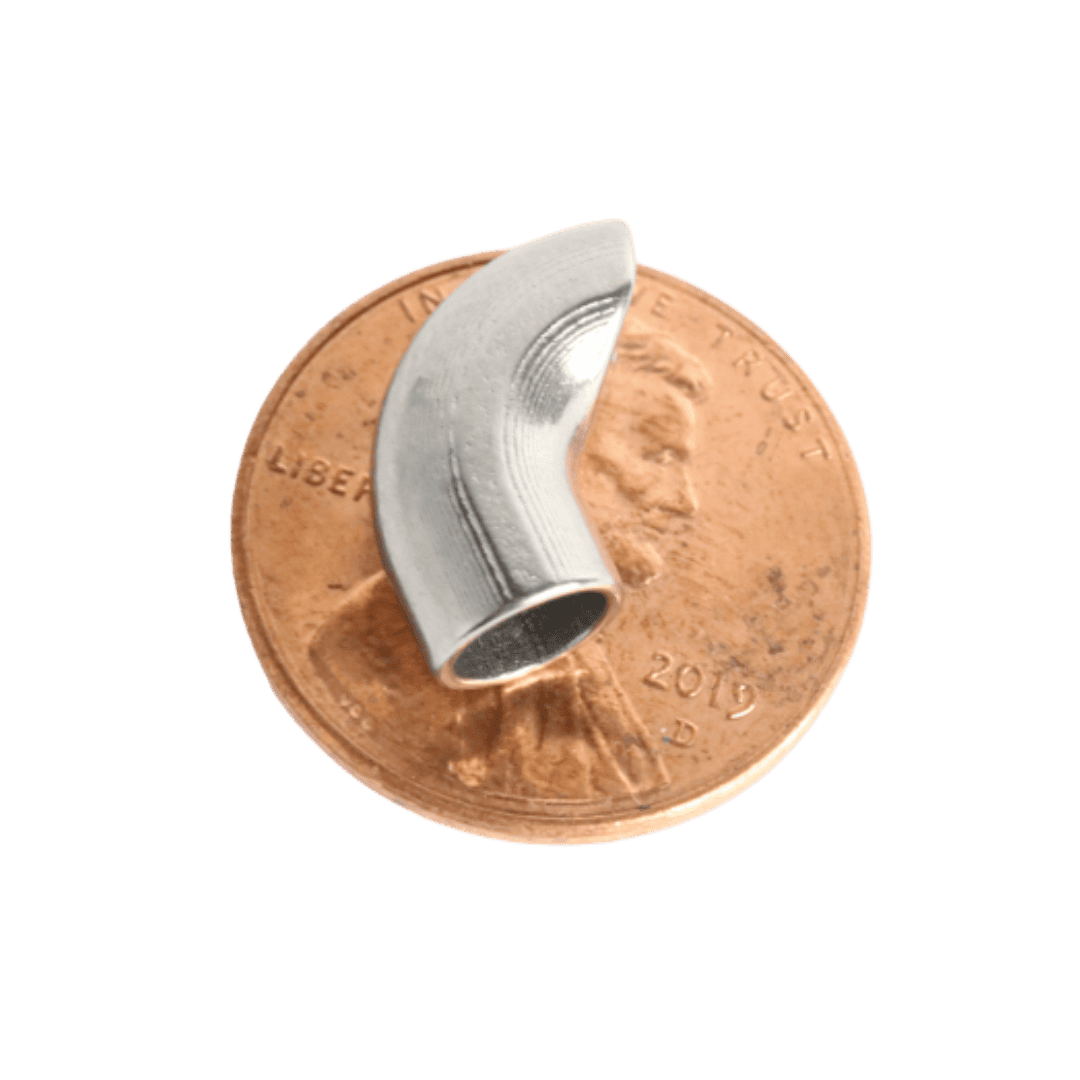
3DEO's Solution
Bone Scraper Price Reduced by 40%
The printers at 3DEO were capable of bringing the price per piece down by 40%, with no tooling costs. 3DEO was able to save the customer $92,500, while also upgrading to superior steel for their surgical device tool tip.
”[3DEO’s] business model allows manufacturers to gain the cost savings, design freedom, and manufacturing flexibility needed to compete - without having to incur millions of dollars for a metal AM machine and the supporting infrastructure.
Metal AM Magazine
Why Manufacturers Choose 3DEO
Short Lead Times
Introduced designs rapidly for fast market entry, with the ability to make design improvements and changes without paying the price of tooling costs.
Flexible Manufacturing
Scaled quantities up/down to match demand; avoided setup and minimum quantity costs with traditional manufacturing.
High Quality Parts
3DEO’s ISO certified parts exceed the MIM industry benchmark, ensuring high-quality parts with the best surface finish in the industry.