CASE STUDY
Linear Ball Screw Application
A linear ball screw is a mechanical actuator that creates high-performance, low-friction linear motion at high speeds and duty loads. Essentially, it is a high-efficiency method of converting rotary motion to linear motion by using a recirculating ball mechanism between a screw shaft and a nut. Compared with a conventional sliding screw, the ball screw requires far less driving torque, typically one-third or less for comparable loads. This makes it ideal for reducing the required drive motor power for a given application. Linear ball screws are widely utilized in a variety of industries: from warehouse logistics robots and automotive power steering to aircraft aileron actuators — or even semiconductor wafer processing equipment stages.
NOTE: This case study is based on 3DEO’s production of the ball return tube for a US-based Tier 3 aerospace supplier in the aerospace and aviation industry.
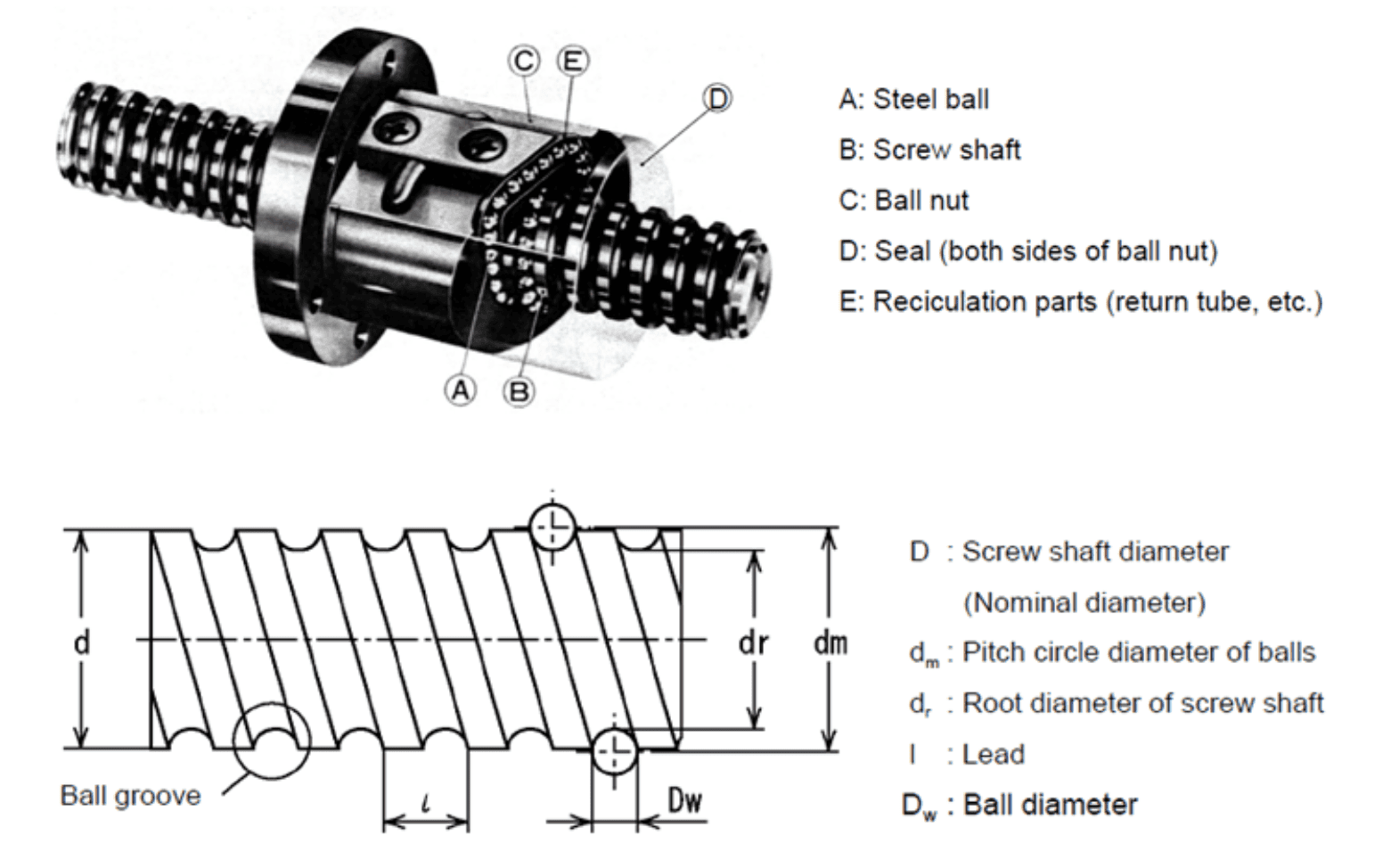
The Challenge - Ball Return Tube
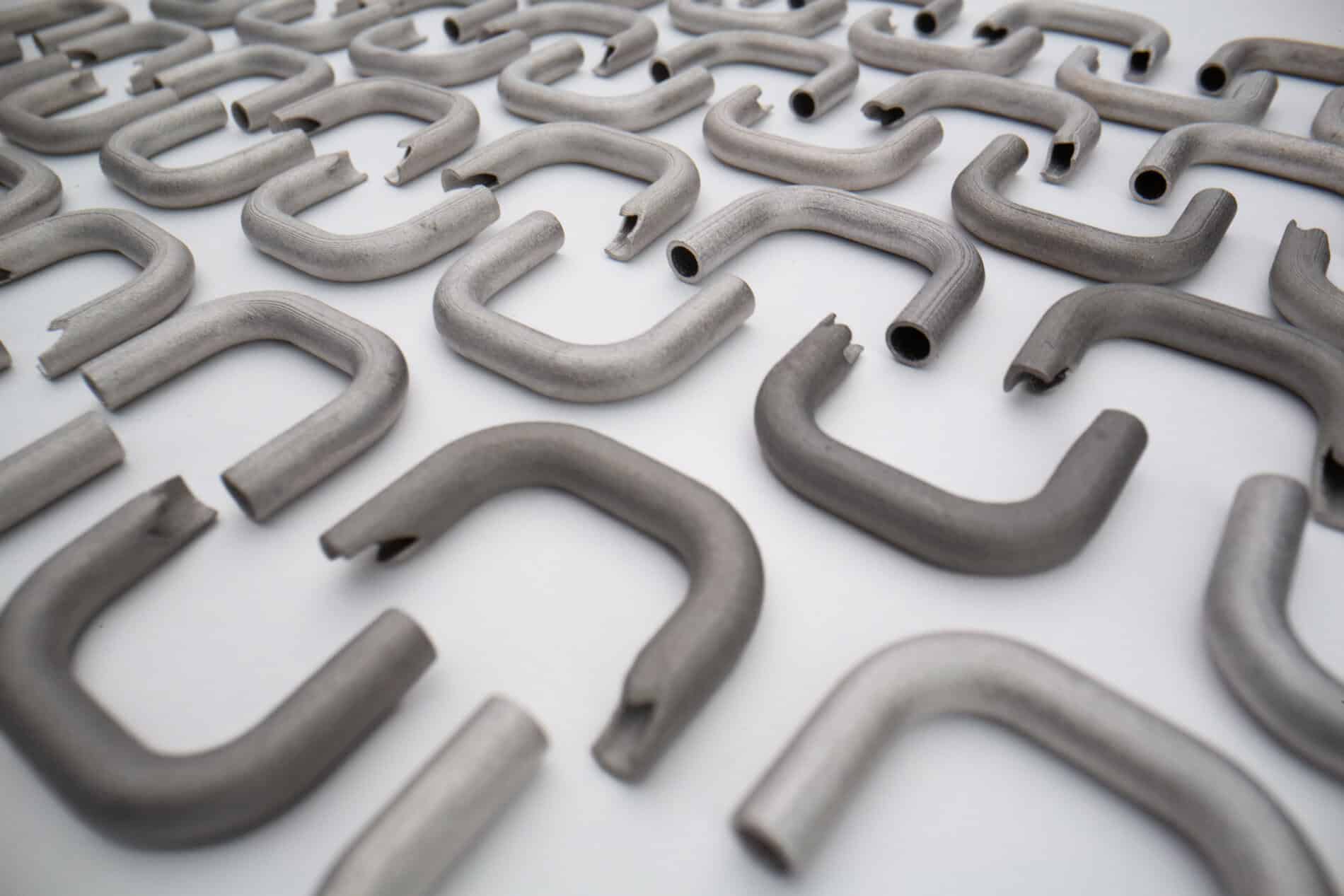
Ball bearings in the ball-nut assembly facilitate low-friction motion but must be recirculated to provide continuous rolling contact. One of the legacy designs for recirculating the ball bearings requires a small, precision bent tube. This tube is particularly difficult to fabricate because of the tight tolerances required on the inner diameter of the tube and the very small bearing size. This particular design recirculates 0.080” ball bearings.
In our customer’s linear ball screw application, the tube was less than 0.65” in its longest dimension. According to them, they could only get a few suppliers to even attempt the part. Conventional suppliers attempted to bend tubing, which would result in crimping and flattening at the elbows of the tube, preventing ball circulation. Since this Tier 3 aerospace supplier could not find a manufacturing partner, they turned to 3DEO and metal 3D printing as a ‘Hail Mary’ alternative.
”We wanted 17-4PH in the application because it is a robust material. The durability of the printed part in the application really impressed our customer.
Lead Engineer
Tier 3 Aerospace Manufacturer
The Solution
3DEO approaches every project as a collaborative partnership, taking a holistic view of our customers’ pain points, objectives, and development needs. The team is driven by its commitment to help engineers solve their toughest problems or do things that haven’t been done before.
In this case, 3DEO’s applications engineering team spent many hours with the aerospace customer to review the design of the ball nut assembly and understand the requirements of the application. They brainstormed through many different creative solutions and in the end, they co-designed and fabricated a superior ball return tube to solve the problem with the customer’s engineering team.
”This was a critical component in the assembly that we could not make any other way. 3DEO partnered with us to deeply understand the application and help us solve the problem, and this collaboration was essential to our success.
President
Tier 3 Aerospace Manufacturer
3DEO worked directly with the customer’s engineering team starting at the design stage to ensure their designs were optimized for 3DEO’s technology—and then in the course of the collaboration, the teams also came up with a creative solution to leverage the geometric freedom of 3DEO’s printers to eliminate an expensive post-machining step, adding further value.
Conventional Process
3 steps: Bend tube, fixture part, machine part
3DEO’s Process
1 step: Print part
Results of Fatigue Testing
Once refined through multiple iterations, the part design was ready for testing.
”Our customer specified that the minimum number of cycles of one ball return tube needed to be 12,000. Legacy ball return tubes were failing between 10,000 and 12,000 cycles. The 3DEO parts ran to 20,000 cycles without a single issue, and we just turned the machine off to end the test. The durability of 3DEO's parts in testing was exceptional.
Lead Program Engineer
Tier 3 Aerospace Manufacturer
Testing threshold:
Minimum 12,000 cycles
Legacy part:
Failed at 10,000 cycles
3DEO part:
No failure, even after 20,000 cycles
In fact, when the fatigue testing was complete and the assembly analyzed, 3DEO’s ball return tube showed less wear than the ball bearings.
Benefits of Working with 3DEO
3DEO is an award-winning design, engineering and manufacturing service provider specializing in complex metal 3D printed components produced at scale. We help companies at every stage of their product lifecycle from ideation to scale, partnering with customers to design and optimize for both additive manufacturing AND their application requirements.
A next-generation American manufacturing technology company, 3DEO is working with many companies today to replace investment cast and machined components and assemblies. In addition to ISO 9001, the company is currently certifying for AS9100.

3DEO is driven by its commitment to help engineers solve their toughest problems or do things that haven’t been done before. Whether you need design expertise to build prototypes that seamlessly transition to scale or are seeking innovative solutions to a complex supply chain, 3DEO can help.
- Early-stage design for additive manufacturing
- Component functionality optimization
- Transition from prototyping to production
- Production at scale
3DEO is an indirect supplier to:
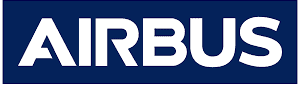

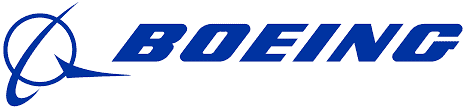
Linear Ball Screw Components Benefitting from 3DEO’s Technology & Services
- Crossover components
- Ball return pipes/tubes
- Ball nuts
- Deflector-type
- End cap-type
Characteristic Ball-Screw Features
Sizes
- Screw Travel Lengths – 1” to 8’ typical
- Screw Diameters – 5mm – 1000mm typical
Pitch
Representative of the angle of the threads. Often represented in distance traveled linearly per revolution of the screw.
Start Count
Commonly 1 to 4 starts, meaning the number of individual bearing races operating in parallel. Related to the pitch and impacts how much operating torque is required and the translation speed of the carriage.
Tolerance
Defined in units of error per unit of distance traveled. For example, if offered in imperial units would typically be inches of error per inch: 001”/1” for a 0.1% linear travel error specification.
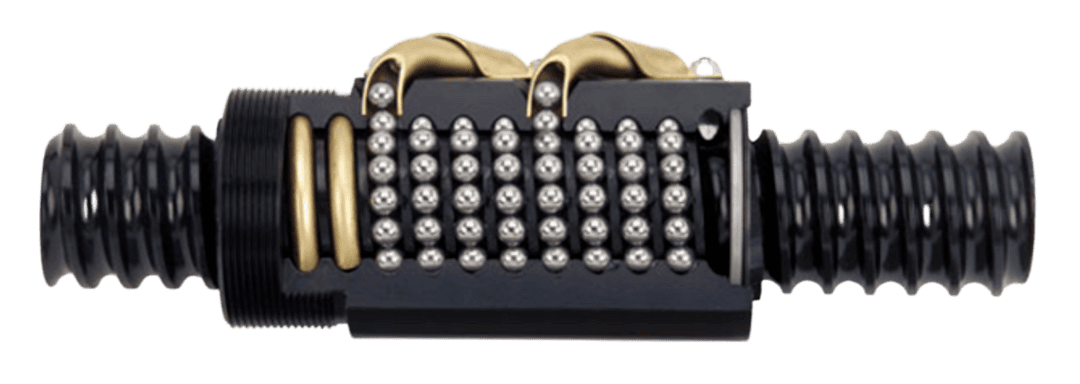